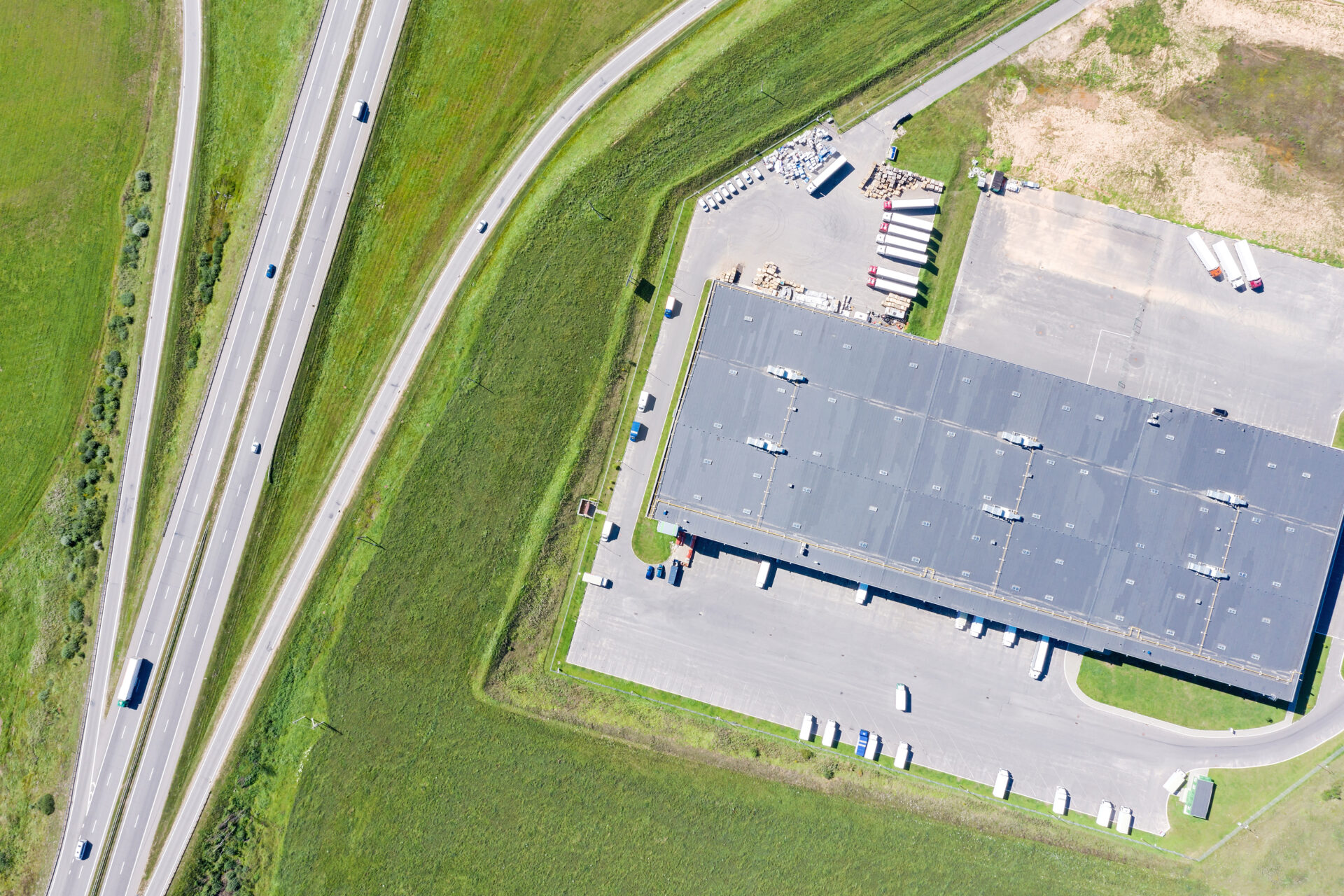
Location search Eastern Europe: The labor market 2025
How attractive is Eastern Europe as a production location in 2025? Find out everything you…
BLOG
In today’s fast-paced world of logistics, efficiency is key to ensuring future competitiveness, especially when it comes to inventory management. Managing inventory manually is time-consuming and error-prone, leading to bottlenecks, inefficient processes and sub-optimal use of available space. Automated warehouse systems, on the other hand, offer companies the opportunity to manage their stock more efficiently and optimize processes. In this article, we take a closer look at the benefits and functionality of automated storage systems and how they can help future-proof your warehouse.
There are numerous systems in the automation of warehouse technology that can be implemented in various stages. A basic distinction is made between manual, semi-automatic and fully automatic storage systems. A wide variety of systems are available on the market from various suppliers. Below you will find an overview.
Manual storage systems are probably the most common type of storage system. Here, the processes within a warehouse take place manually. This means that goods movement, management and handling are carried out manually by employees. Manual storage systems are easy to handle and set up, have a high degree of flexibility and are cheaper to invest in than automated storage systems. However, manual storage systems are not more cost-effective in terms of total cost of ownership (TCO) above a certain operating point. The biggest cost driver for manual storage systems is usually the additional personnel required. Furthermore, manual systems can quickly lose efficiency and performance with large quantities of goods or complex inventories.
Semi-automatic storage systems are characterized by the fact that warehouse employees are supported by technology, but perform some activities manually. For example, the picking of goods in a pallet rack is supported by a storage and retrieval unit (SRU). The employee stands on the RGB, can drive to the storage location and carry out picking from the rack by hand. In practice, this is still common today, especially in narrow-aisle warehouses. Semi-automatic systems often represent a preliminary stage of fully automatic systems.
As the name suggests, fully automated storage systems are characterized by the fact that no manual intervention from outside is required to carry out work cycles. The fully automated systems operate completely independently without any intervention by the employee. The requirements for a fully automated storage system are high. On the one hand, depending on the storage system, there are requirements for the building and the environment, and on the other hand, high safety standards must be met. There are various fully automated systems on the market, such as pallet warehouses with storage and retrieval machines, shuttle systems, Autostore and Kardex systems. In the course of our blog series, we will present some of these fully automated storage systems.
Based on the storage systems described above, the basics of various automated storage systems are now presented. Some storage systems are used for both pallets and small load carriers. Industry-specific storage systems for very large and heavy products, for example, are also not uncommon.
The following table provides an initial overview. Here, the stored goods can be compared and evaluated with different storage systems. You can find out how the evaluations result in the detailed considerations of the storage systems.
Automated pallet warehouses store, transport and remove pallets using automated systems. These warehouses use storage and retrieval machines, conveyor technology, shuttle systems or automated guided vehicles (AGVs) to move pallets efficiently and without manual intervention. They are characterized above all by high space utilization and handling capacity. Automated pallet racking systems can be built up to 50 m high and enable high performance. These systems use various technologies to optimize and, above all, automate the storage and retrieval of pallets.
These include the following technologies:
With the technologies mentioned, a warehouse management system is absolutely essential, which provides all information regarding the stored products, storage and retrieval, stock, etc. Automated pallet warehouses are often used in large logistics centers, production facilities or in e-commerce, where a high storage density, higher storage capacity, faster processes and a smooth material flow are required. In addition, these storage systems are increasingly being used in companies that can find fewer workers for their operations due to the tight labor market. Although automated pallet warehouses are more expensive in terms of initial investment, they have lower operating costs due to reduced personnel requirements and lower error rates in the process.
Similar to automated pallet warehouses, automated small parts warehouses are highly specialized storage systems that can be used for the storage, management and picking of small individual parts and components. The main load carriers are standardized small load carriers. Automated small parts warehouses are space-saving and compact warehouses that store goods on several levels. Automatic small parts warehouses are also characterized by high access speed, fast picking and just-in-time deliveries. There are various storage systems on the market that use different technologies such as automated small parts warehouses (AKL), AutoStore, shuttle systems and carousel and vertical lifts.
When does which technology make the most sense?
Typically, IT systems take over the control and monitoring of warehouse processes. A central component is a warehouse management system, which contains all information relating to the stored products, storage and retrieval and the inventory. Automated small parts warehouses are frequently used in industry, production, the automotive sector, pharmaceutical and medical technology and e-commerce. Automated small parts warehouses are particularly useful in industries that have to handle a large variety of small items.
Automatic special storage systems are usually specifically adapted to the stored goods. Nevertheless, these storage systems can range from manual to fully automated. If the stored goods do not fit on standardized load carriers such as Euro pallets, industrial pallets or common small load carriers, the choice falls on special storage systems. Warehouse manufacturers adapt their standardized storage systems to specific requirements. The hardware behind automated special warehouses can be identical to the classic automated warehouse systems. Special warehouses can be operated by robots, conveyor technology, storage and retrieval machines or automatic crane systems in order to create optimized and efficient warehouse processes.
Storage systems that require a standardized load carrier, such as shuttle systems or an Autostore, are not suitable for special warehouses. Such a special warehouse can be used, for example, for long goods, heavy industrial equipment, large machine components or other specific materials. Automation in warehouse operations enables greater flexibility and faster, error-free handling of special goods that are often difficult to store and move manually. In addition, automated storage systems can achieve a very high storage density compared to manual systems, thus reducing space requirements.
Automatic long goods warehouses are a common type of special warehouse. These are specially developed for the storage and management of long goods. These include materials such as metal pipes, profiles, wooden slats or steel beams. A fundamental distinction in the design of a long goods storage system is whether the part is to be accessed from the front or the long side. With frontal access, companies store the materials in channels. This type of storage is called honeycomb racking. If the stored goods are accessed from the long side, a cantilever rack or a rack design can be selected. For all long goods storage systems, it is important to ensure that the working area in front of the rack is sufficiently large so that the stored goods can be removed and moved without collision. Long goods storage systems are mainly used in the steel industry, in the construction industry and by suppliers of building materials.
The materials are stored either horizontally or vertically, with horizontal storage being used much more frequently. To ensure safe and efficient storage, the materials are usually stored on shelving systems or in shelving compartments. To achieve space-saving storage, mobile racking systems are often used in manual long goods warehouses. Mobile racking systems are no longer used in automated warehouses. Long goods warehouses are mainly used in the steel industry, in the construction industry and by suppliers of building materials.
Another storage system is the automated large parts warehouse. These are specially developed for the storage and management of large and heavy goods such as sheet metal or steel structures. For companies that need to store and move large components with high density, a high degree of automation makes sense. Manual or semi-automatic solutions are very limited in the utilization of the room height and increase the risk potential when handling large and heavy components. Technologies such as automated high-rack stackers or operating devices for racks and towers are used to move the stored goods.
Typical features of an automated special warehouse are
Automatic special storage systems are primarily used in industry, logistics centers and large production facilities where the storage of special or heavy materials is required.
Automated storage systems are fundamentally changing the way companies organize their warehousing and material flows. Customized solutions and the use of state-of-the-art technology enable a significant increase in efficiency, capacity and flexibility in warehouse management.
Invest in such technologies in good time to improve your logistics processes and make them future-proof. The selection of the right system and its design depends on the specific needs and objectives of your company.
Senior Manager,
The industrial engineering graduate advises his clients on issues relating to warehouse and logistics planning and the digitalization of logistics (particularly in the ERP, WMS and TMS environment). He also provides clients with comprehensive support in the areas of operations management and strategy.