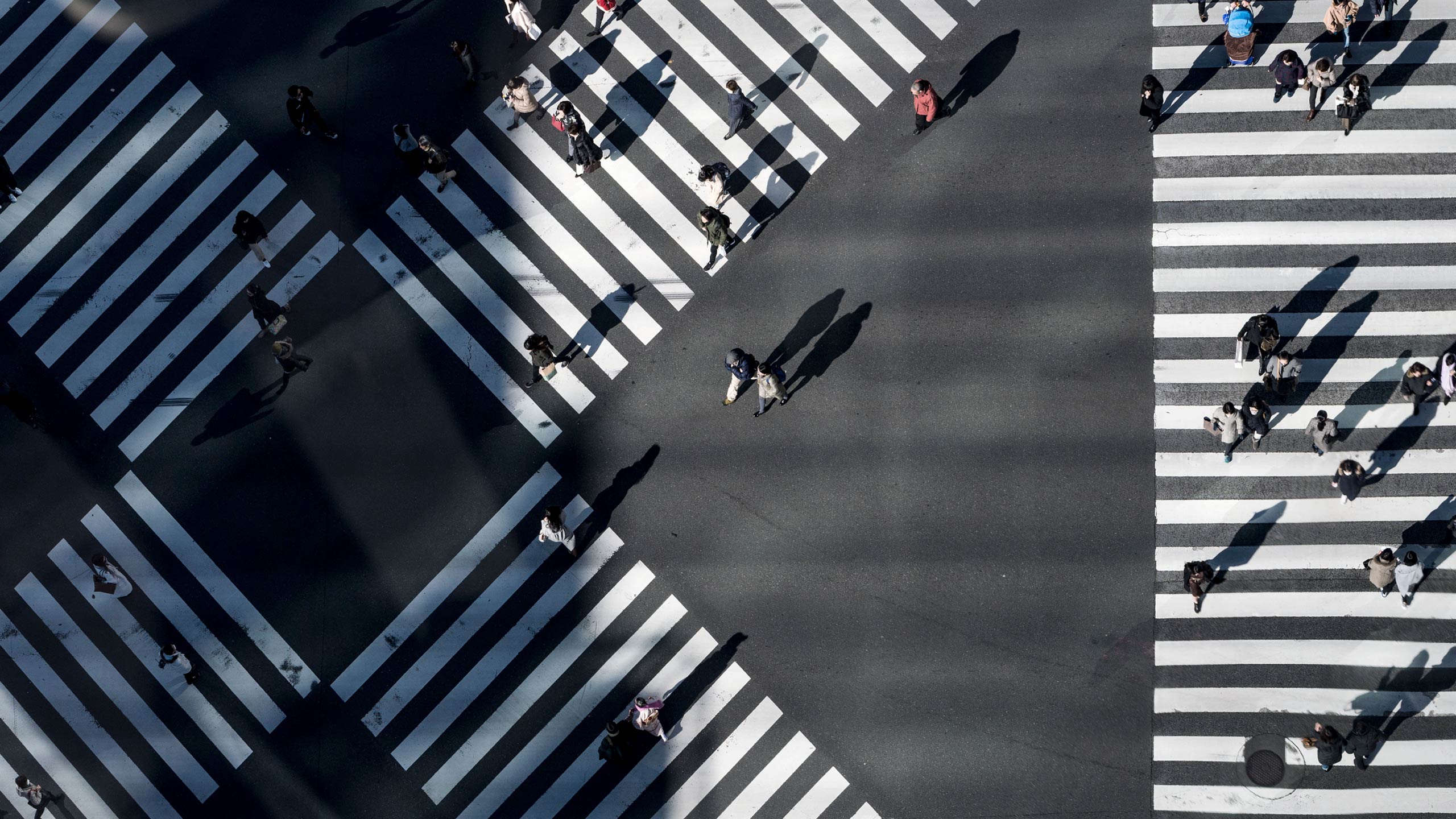
Production location Eastern Europe: The labor market
Even after two decades of economic upturn, the countries of Eastern Europe remain an attractive…
BLOG
Efficient spare parts logistics is crucial for industrial companies that distribute and produce spare parts. Customers expect high availability of important spare parts at optimized costs. Manufacturers and suppliers must design their processes in their network in such a way that they can react flexibly and quickly to changing requirements without unnecessarily increasing storage and logistics costs.
In spare parts logistics, competitiveness is no longer determined solely by availability, but also by the ability to respond flexibly and cost-effectively to market requirements with intelligent and data-driven processes.
Phillip Carl, Senior Manager Logistics Division
The use of modern IT systems, automation and data-based forecasts makes it possible to optimize inventories, shorten procurement times and lead times and make the entire supply chain more flexible. The targeted combination of digitalized production, warehouse and ordering processes, intelligent demand planning and an efficient distribution network enables manufacturers and suppliers to strengthen their market position in the long term. The global market volume of spare parts logistics is expected to grow at an annual rate of over 3% from the current 47 billion euros to over 60 billion euros.
A comprehensive understanding of customer needs is crucial in order to provide a competitive spare parts offering. Manufacturers and suppliers should carry out detailed analyses of operating conditions, maintenance histories and machine data in order to tailor services precisely to specific customer requirements.
The lead time plays a central role here. The entire time from the moment the customer recognizes the need to the physical availability of the spare part is relevant. An efficient process chain – from identification of the defective part to ordering and, if necessary, production through to delivery and documentation in the digital twin – can significantly reduce this lead time.
Structured recording and evaluation of the installed base not only makes it possible to forecast future spare parts requirements more precisely, but also to develop customized and competitive service offers. A data-driven approach creates transparency about market changes and trends, allowing industrial companies to act flexibly and with foresight.
A particular focus should be on identifying critical spare parts – those components whose failure would have a significant impact on customer production. Manufacturers should rely on data-based analyses to build up targeted stocks and provide proactive spare parts packages or kits.
In order to better understand customer requirements and optimize the spare parts strategy, the following key questions should be considered:
The continuous optimization of business models and distribution concepts in spare parts management is a key lever for increasing efficiency and reducing costs in spare parts logistics. One of the biggest challenges is to find the right balance between storage costs, delivery speed and security of supply. Manufacturers must therefore carefully weigh up the advantages and disadvantages of centralized and decentralized warehouse structures. While central warehouses enable lower inventory costs, for example, decentralized structures offer greater responsiveness in the event of unplanned machine failures on the part of customers.
Spare parts management is increasingly developing into an independent business model, which in some industrial companies, especially in mechanical engineering, is even managed commercially in a separate company. This requires targeted management of warehousing, logistics and pricing strategy in order to ensure both profitability and long-term customer loyalty. At the same time, original manufacturers of spare parts are in direct competition with “no-name” suppliers, who often offer individual parts at lower prices. To hold their own in this competitive environment, many OEMs are turning to digital services that emphasize the added value of their products. One effective solution is to provide a digital twin of the customer’s system: the customer can use this digital image to quickly and easily identify and order the right spare parts in the web store – including all necessary additional components such as gasket sets. This not only optimizes the ordering process, but also ensures the use of high-quality and compatible components. As a result, companies reduce downtimes and maximize machine availability.
By strategically combining different distribution concepts, industrial companies can reduce their operating costs, improve the availability of critical spare parts and thus minimize downtimes – a decisive competitive advantage in the global market. Strategically placed warehouse locations enable manufacturers to implement just-in-time concepts and provide spare parts in line with demand. Logistics planning tools support companies in location analysis so that they can position warehouses in a cost-efficient and customer-oriented manner. A flexible distribution network also ensures that seasonal fluctuations or unexpected changes in demand are effectively cushioned.
In order to improve business models and distribution strategies in a targeted manner, manufacturers should analyze the following aspects:
Digital transformation and the comprehensive integration of modern IT systems are key building blocks for efficient and resilient spare parts logistics. Digital tools enable precise recording, categorization and allocation of spare parts to machine components. At the same time, AI-supported technologies such as process mining and digital twins create new opportunities by predicting spare parts requirements, automating orders and thus speeding up processes.
For manufacturing companies, efficient control of warehouse processes in spare parts management is essential to ensure high availability and optimize costs at the same time. The use of a modern and powerful warehouse management system (WMS) offers decisive advantages here: Companies that rely on modern WMS can not only reduce costs, but also increase their competitiveness by acting faster, more efficiently and in a more customer-oriented manner. One solution that aims to optimize inventory management and extensively automate warehouse processes is SAP EWM, for example. Under SAP S/4HANA, Stock Room Management (SAP SRM) is also available as a lean alternative for smaller, manually operated warehouses. While SAP EWM is specially designed for complex, highly automated warehouses, Stock Room Management enables the efficient handling of basic processes such as goods receipt, goods issue and inventory management – ideal for companies that require a compact and easy-to-implement warehouse management solution.
A WMS offers a wide range of functions that support companies in making their warehouse processes more efficient:
For manufacturers of spare parts, a state-of-the-art logistics center with automated warehouse processes is the key to higher efficiency and greater capacity. Technologies such as automated guided vehicles (AGVs), automated high-bay warehouses and robot-assisted picking systems reduce manual effort while increasing the speed and precision of processes.
Through the targeted use of warehouse automation technologies, manufacturers can optimally control their inventories and intelligently coordinate material flows. Cloud-based solutions enable dynamic inventory management and ensure maximum space utilization. An optimized warehouse architecture with well thought-out material flows also ensures that critical spare parts are available quickly.
In addition to cost savings through reduced storage space, these technologies offer greater process reliability and improved traceability. In combination with high-performance warehouse management systems (WMS), automated warehouse solutions create the basis for efficient, flexible and resilient spare parts logistics.
The digital transformation in spare parts logistics is being driven forward significantly by the use of process mining. This technology makes it possible to analyze processes in spare parts logistics in detail and uncover potential for optimization. By evaluating data from existing systems, inefficient processes can be identified, bottlenecks made visible and targeted measures for process improvement implemented. Especially in conjunction with modern ERP systems such as SAP S/4HANA, companies can automate and seamlessly integrate their production, ordering, warehousing and shipping processes to ensure a fast and reliable supply of spare parts.
Another important component is the Digital Twin – a digital image of the entire distribution network. This virtual model enables manufacturers to monitor and simulate their warehouse structures and logistics processes in real time and make strategic decisions based on data. In this way, questions regarding the optimal choice of location for spare parts warehouses, the decentralization or centralization of stocks and the number of storage levels required through to the design of the transport network can be answered on a sound basis.
The aim of these technologies is to make the spare parts logistics network more efficient, maximize the availability of critical parts and reduce storage costs at the same time. With process mining and the digital twin, manufacturers can run through and evaluate various scenarios and optimally adapt their logistics to the specific requirements of spare parts supply.
Specific questions need to be answered in order to successfully drive the digital transformation forward:
In a world of global supply chains and volatile markets, effective risk management is essential to ensure long-term stability and supply capability. For manufacturers of spare parts, this means identifying and assessing potential risks at an early stage and minimizing them with targeted measures. Looking at the product life cycle as a first step helps to determine when a manufacturer will have an increased need for spare parts. However, specific tools and solutions are required for subsequent, more detailed steps. Diversifying the supplier base, establishing flexible logistics processes and strategic safety stocks for critical components are decisive measures for avoiding supply disruptions and at the same time being prepared for unforeseen events.
Modern forecasting tools enable manufacturers to identify material requirements at an early stage and make informed decisions. However, resilient spare parts logistics is not only based on technological solutions, but also on close cooperation with strategic suppliers. Clear agreements on delivery times, escalation mechanisms and contingency plans increase crisis resilience and strengthen trust along the entire value chain.
Flexible and agile spare parts logistics are crucial in order to react quickly and effectively to market fluctuations or unexpected supply bottlenecks. Manufacturers should continuously analyze critical points in their supply chain, implement risk mitigation mechanisms and regularly adapt their processes to new challenges.
The implementation of a supply chain control tower can be a helpful tool for minimizing risk. This digital control system integrates real-time data from various sources and creates transparency across the entire supply chain. This enables manufacturers to identify potential risks at an early stage, eliminate bottlenecks more quickly and optimize logistics processes in a targeted manner. The use of a supply chain control tower makes it possible to make supply chains more resilient and at the same time leverage efficiency potential – a useful addition for companies that want to further develop their risk strategy.
To strengthen risk management and increase flexibility, companies should address the following key issues:
Choosing the right transportation strategy is crucial in order to optimally balance costs, speed and reliability. Manufacturers benefit from multimodal transport solutions in which different modes of transport – such as truck, rail, sea or air freight – are combined in a targeted manner to achieve maximum efficiency and flexibility.
Digital technologies play a central role in this: IoT-supported real-time tracking systems enable continuous monitoring of transports, allowing delays to be detected at an early stage and countermeasures to be initiated. In addition, modern transport management systems (TMS) facilitate route planning, capacity control and collaboration with logistics service providers.
In addition to transport optimization, compliance with trade and customs regulations is also a key success factor. Efficient customs clearance processes and the use of digital customs systems minimize delays and reduce costs. Companies involved in the international spare parts trade must also ensure that they meet all regulatory requirements.
Optimizing the organizational structure is particularly effective as part of a cost-cutting programme, as it uncovers and eliminates inefficiencies. Unclear responsibilities, duplication of responsibilities and too many hierarchical levels often lead to unnecessary costs and delays. A realignment can streamline processes, simplify structures and deploy resources in a more targeted manner. This not only reduces operating costs, but also increases the agility and efficiency of the company.
Optimizing the organizational structure is particularly effective as part of a cost-cutting programme, as it uncovers and eliminates inefficiencies. Unclear responsibilities, duplication of responsibilities and too many hierarchical levels often lead to unnecessary costs and delays. A realignment can streamline processes, simplify structures and deploy resources in a more targeted manner. This not only reduces operating costs, but also increases the agility and efficiency of the company.
Senior Manager Logistics
Do you need support in optimizing your spare parts logistics, integrating digital technologies or developing a flexible and cost-efficient strategy? I look forward to hearing from you and will be happy to develop solutions for your challenges together.
Efficient spare parts logistics is crucial to ensure your competitiveness as a manufacturer or supplier. Through the targeted analysis of customer requirements, the optimization of your business models and the integration of digital technologies, you can make your processes more flexible, reduce costs and ensure the availability of critical spare parts. Proactive risk management also strengthens the resilience of your entire supply chain.
Senior Manager,
The industrial engineering graduate advises his clients on issues relating to warehouse and logistics planning and the digitalization of logistics (particularly in the ERP, WMS and TMS environment). He also provides clients with comprehensive support in the areas of operations management and strategy.