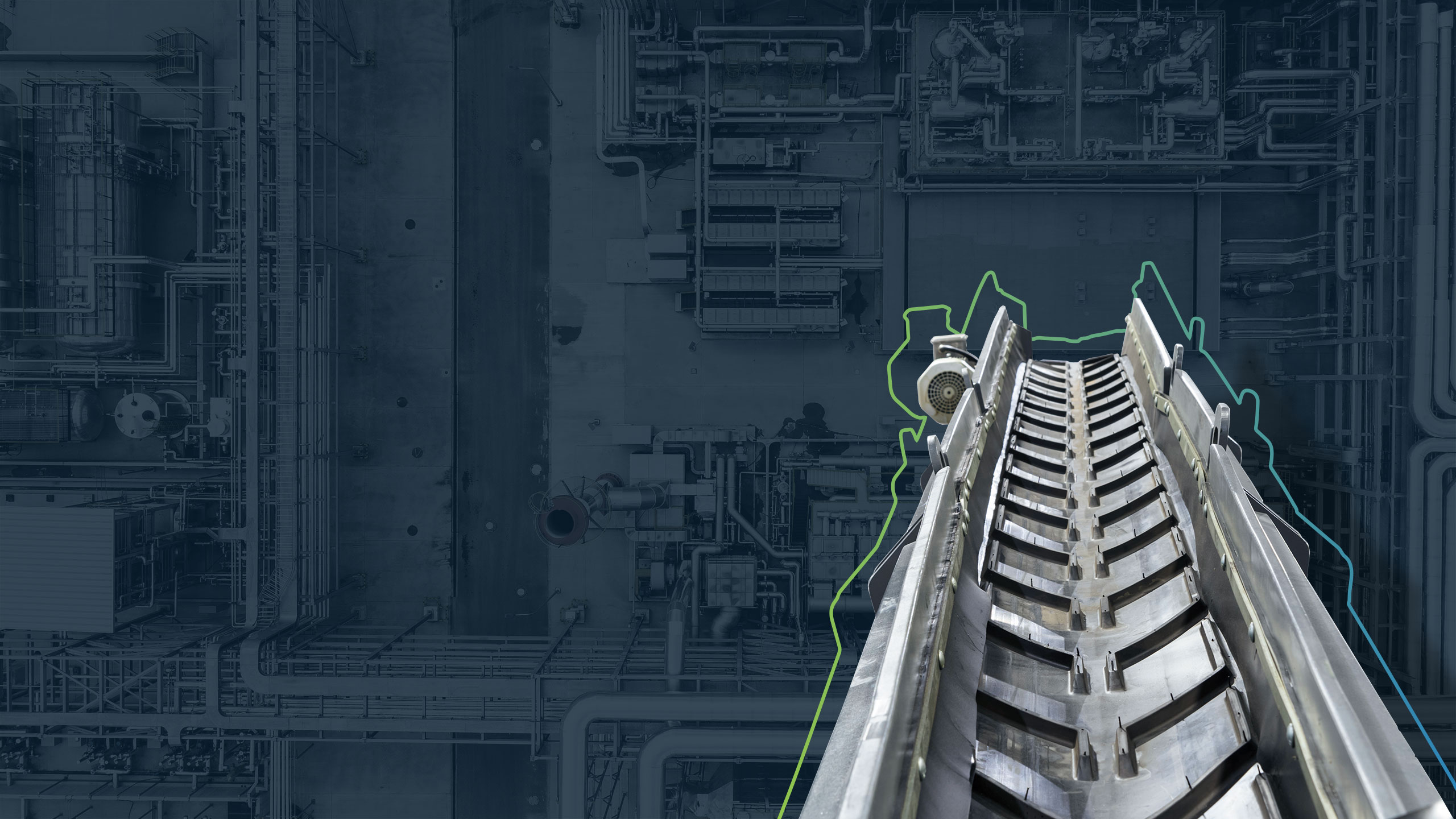
efficiency management
Increasing efficiency: working systematically and more productively
Optimize the use of resources and processes in a targeted and controlled manner
Increasing efficiency in day-to-day operations is a complex task for any business – a wide variety of factors may prevent you from quickly deciding which aspects and processes are really hindering productivity. In every business area, there are different challenges that need to be identified, understood and overcome.
Problems often arise unnoticed
A lack of effectiveness is often based on developments that have arisen organically as a result of changes in the company. Perhaps new tasks and products have been added, but there has not been time to thoroughly adapt those processes that were only indirectly affected by these innovations.
Or a department could and had to grow rapidly in a relatively short time due to the success of a product – but now it turns out that there is a lack of suitable structures for the larger number of employees and cooperation with neighboring business units no longer works properly.
The causes lie in the system
From our many years of experience in the field of technical management consulting, we know that such problems are usually caused by systemic weaknesses. This includes these seven issues in particular:
- Unclear and non-transparent processes: If operational processes are not clearly defined and documented, there is always confusion and delays in the processes.
- Inadequate resource management: If the company does not have a precise overview of which resources and how much energy are required at which points, this means that production capacities cannot be used optimally. This wastes both resources and energy – and that costs money.
- Outdated technologies: Outdated production facilities and IT systems as well as software that is no longer state of the art can put you at a significant competitive disadvantage compared to your competitors.
- Inefficient supply chain management: Inadequate coordination between suppliers and production planning can lead to your supply chain having too little resilience to disruptions. Delivery bottlenecks or unreliable suppliers can quickly become a problem.
- Lack of flexibility: The more rigid your production structures are, the more difficult it is to adapt to new market requirements – even sudden fluctuations in demand for individual products may not be handled well.
- Insufficient quality control: If quality problems occur with your products, this requires additional work and increases costs – in the worst case, it also jeopardizes your reputation.
- Lack of qualified staff: If employees do not have the necessary training and qualifications to carry out their work correctly and use modern technologies, this will also affect efficiency. In addition, many processes are not designed for less qualified employees.
Systematic and holistic: how to increase efficiency
It is important and sensible to take a close look at potential challenges in all these areas. However, in order to tackle the difficulties, it makes sense not to address them individually, but to take a systematic and holistic approach.
What is increased efficiency? A definition
Increased efficiency describes targeted and systematically planned measures to optimize work processes, resource use and business practices in a company with the aim of achieving higher productivity with the same use of resources.
From our practical experience, we know that increasing efficiency is particularly successful when the measures are considered holistically from certain aspects.
Our approach therefore focuses on the topics of operational excellence, sales and operations planning and digital transformation. Finally, the innovative method of process mining makes it possible to tackle the challenges in a targeted manner and on the basis of sound data.
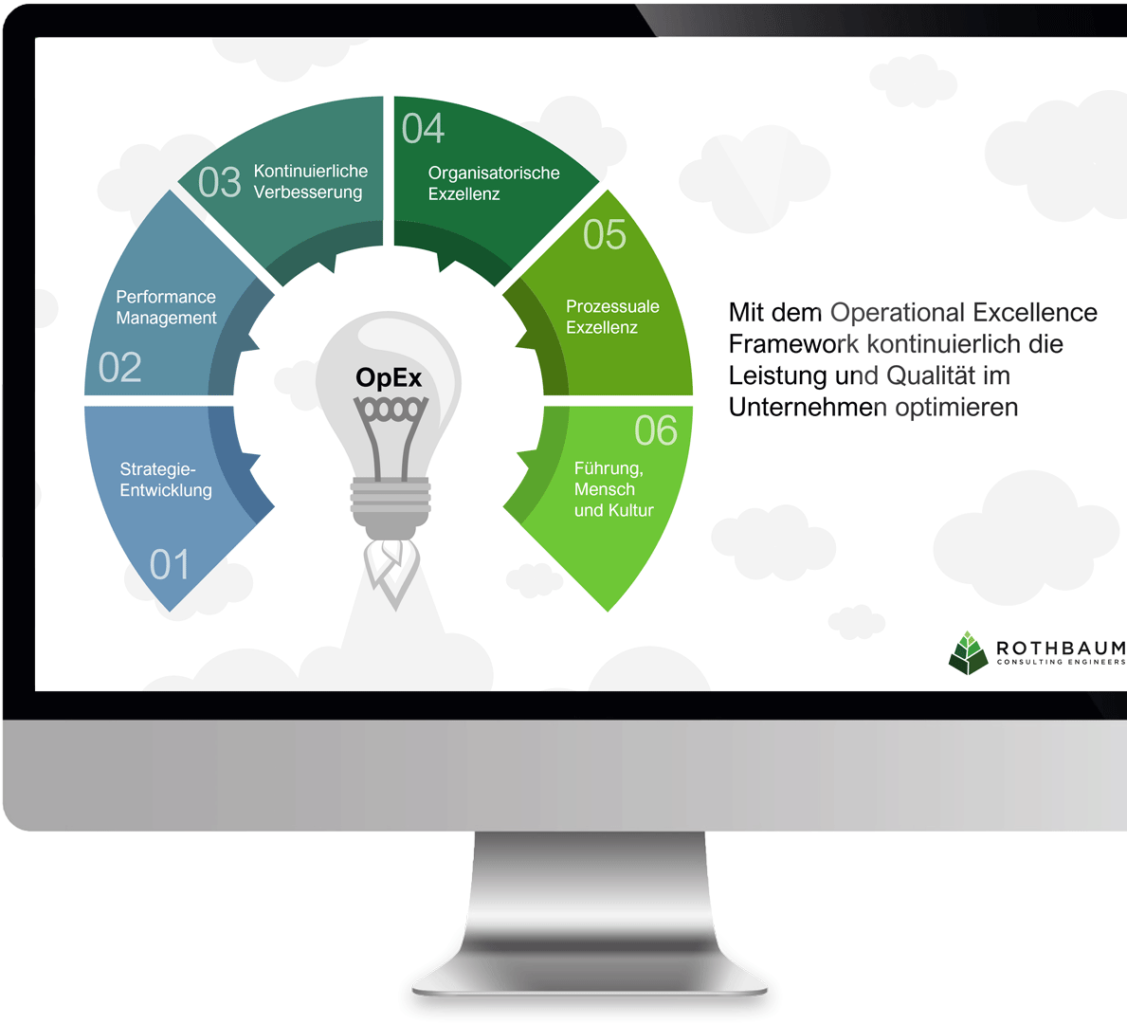
Operational Excellence
The aim of Operational Excellence is for your company to firmly establish processes that ensure the continuous and sustainable improvement of your operations – across the entire value chain. Organizational development then becomes an integral part of your work: quality management through a tailor-made continuous improvement process (CIP), the objectives of which are fed directly from your corporate strategy.
We use proven methods and modern tools to help you improve your operations sustainably and continuously and make them more efficient.
How we proceed:
- Objective analysis of value creation processes, identification of potential for improvement
- Development of a suitable, individual strategy
- Optimizing effectiveness and improving performance – targets, standards, risk management
- Development of a continuous improvement process and promotion of a culture of continuous improvement in all areas of the company
- Analysis, modelling, simulation, optimization and standardization of operational processes
Sales and Operations Planning
Sales and operations planning is about optimally coordinating sales and production planning on the one hand and procurement and financial planning on the other. The aim of these measures is to ensure that you use your production resources efficiently while at the same time increasing customer satisfaction and delivery reliability.
Our steps to get there:
- Development of a customized planning process and project roadmap
- Selection and introduction of suitable tools for analyzing real-time data and creating planning scenarios and forecasts
- Well-founded forecasts and planning processes for close and effective coordination of sales and production
Digital transformation
The successful digitalization of business processes is an essential prerequisite for many approaches to modernization and operational excellence.
We are happy to support you in the digital transformation – with a clear view from a strategic perspective that takes a holistic view of your company and at the same time with both feet on the ground – we have a wealth of experience and many helpful tips and techniques on how to accompany your employees through this change via change management.
In this way, real challenges and problems can be tackled gradually and sensibly in all areas of work without forgetting the interrelationships.
What we can do for you:
- We determine the status quo of your digitalization and develop a digitalization strategy together with you on this basis
- This results in concrete use cases and customized steps for each business area
- We work with you to select the right software and IT systems for your requirements
- We support and manage the transformation from strategy to practical implementation
Process Mining
Especially after successful digitalization, process mining offers you the opportunity to gain full transparency of the real processes in your company in real time. This creates the basis for detailed analyses and specific improvement steps – for greater efficiency and lower costs.
We offer you customized solutions in operations, including for specific processes in production and logistics, because we combine technical expertise in process mining with operational knowledge of business processes in countless different companies.
We advise you from the initial considerations to the implementation of the findings:
- Analysis of the system landscape and the potential for increasing efficiency with process mining
- Development of a roadmap based on initial analyses
- Recording and visualization of existing processes
- Expansion of analyses and visualizations based on specific use cases for real-time monitoring
- Data evaluation for specific measures to increase efficiency and optimize processes
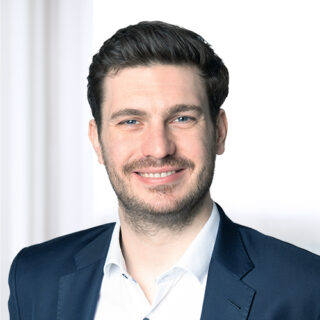
Philipp Kappus
Head of Production
Talk to us!
Do you have any questions about our services in the area of efficiency enhancement or a specific project inquiry? Then please send us a message and we will get back to you as soon as possible.