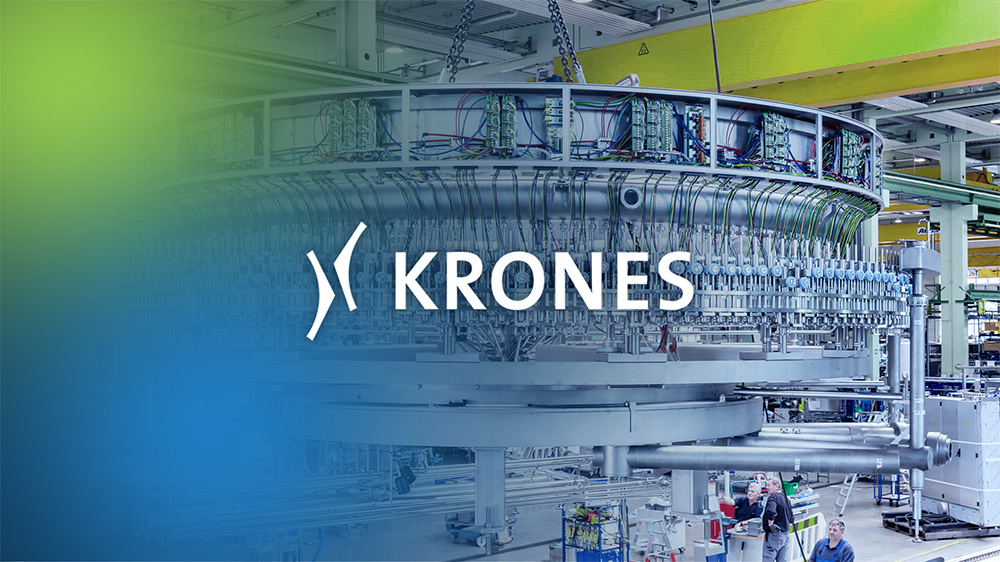
Process mining to optimize order processing
Process mining was used to create a digital image of the processes in the lifecycle…
Success story
Process mining was used to create a digital image of the entire production process and thus generate transparency about the process sequences. The real-time analyses generated – including in the areas of system performance, master data, rejects and idle times – were used to identify weak points and highlight the potential for optimization.
Thanks to Rothbaum’s process mining and operations expertise, we quickly created the process transparency that helps us to optimize waiting and throughput times.”
Harald Valentin, Head of Production Planning
Prüm operates a very complex, multi-stage production process in order to meet the requirements of product diversity. Although the processing steps on the machines are largely automated, all other steps are carried out manually. The idle and transport times significantly exceed the pure processing times. Prüm stores the feedback data from the machines in its own system in order to answer queries and carry out analyses. Due to the high level of complexity, classic analysis options are limited. The possible applications of process mining should therefore be investigated in a pilot project.
Rothbaum created a Celonis data model in close collaboration with experts from production. In joint walkthroughs, weak points in the process were identified and use cases developed. Finally, the results were summarized. Based on these, the decision was made to introduce the software.
Despite major data challenges, together we succeeded in creating a valid digital image of the production process. Based on this data model, it was possible to develop analyses in the areas of system performance, target/actual path comparison and the review of replenishment times. These analyses form the basis for answering the most important recurring questions quickly and effectively.
In the further course of the project, new findings with enormous potential were generated with the loss analysis per system and a delivery time analysis. This can be used in the future, for example, to reduce the idle times of time-critical orders determined in real time by means of rule- or AI-based prioritization – and thus better meet delivery deadlines.
Head of Digital Operations
Do you have questions about the Success Story or Process Mining? Or do you have a specific project inquiry? Send me your message and I will get back to you as soon as possible.