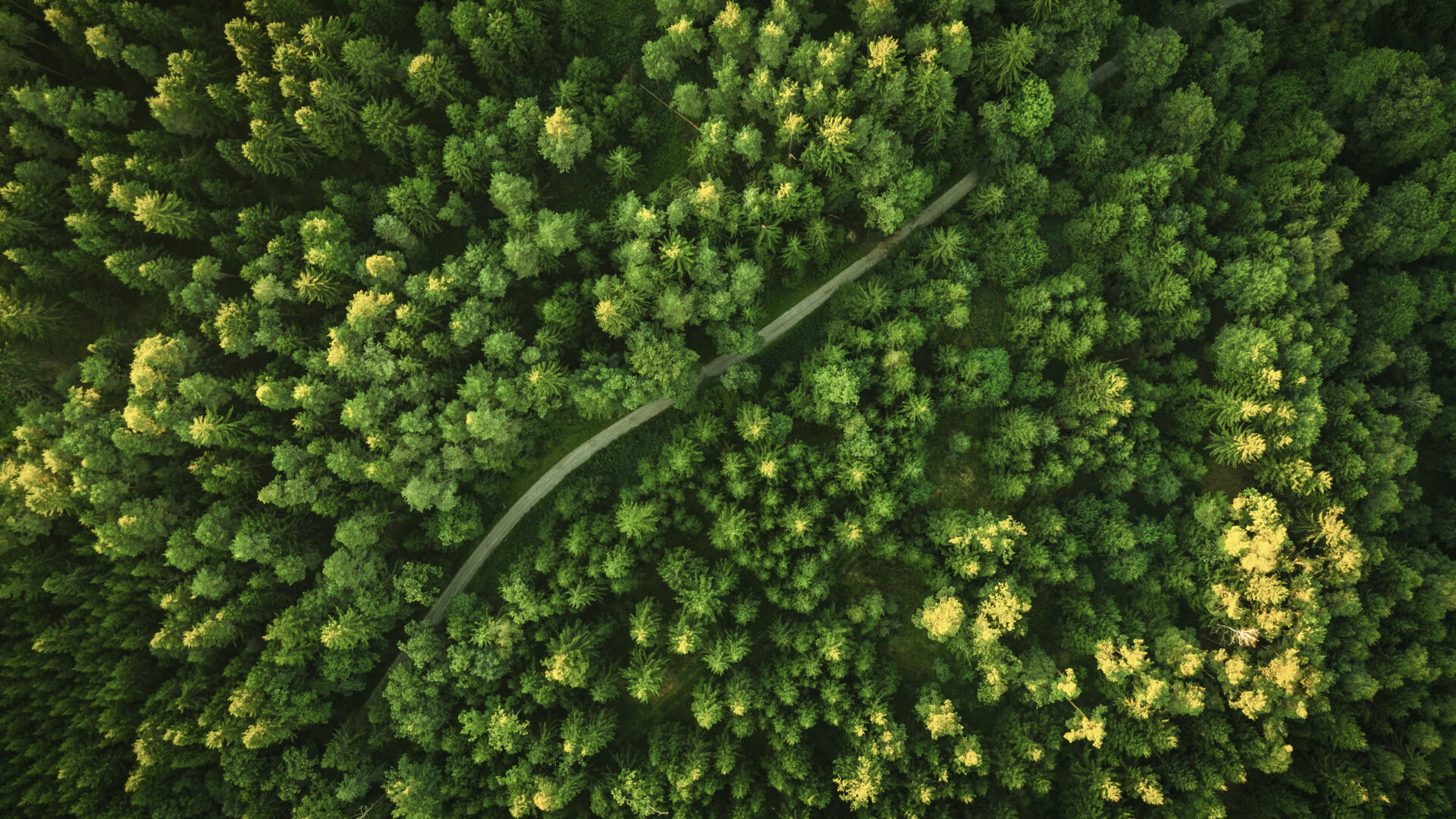
Sustainability in production, logistics and supply chain
Sustainability in operations not only offers the opportunity to make a positive contribution to society…
Blog
Artificial intelligence, autonomous production, smart factory: do you sometimes lose track in the flood of buzzwords and trends? We summarize selected and current digital trends for operational excellence and outline possible applications.
Is your production or logistics “excellent”? Especially in Germany, a high-wage country, efficiency and improvements in effectiveness are decisive competitive factors. You should therefore continuously review the use of the latest tools in order to gain an advantage over your competitors. However, not every trend makes sense and it can be both exhausting and uneconomical to take the position of “first mover”.
In general, operational excellence should always serve customer benefit. So always put yourself in your customer’s shoes. This can be both an internal customer (e.g. another department in the company) and an external customer. If you initially focus on your core processes and see operational excellence as continuous improvement (similar to Six Sigma and Lean Thinking), you are already doing a lot right.
In this article, I will give you an insight into the following trends for operational excellence:
You don’t have to be able to explain all the terms. It is sufficient if you keep an overview and identify the important trends for your operations and check their use.
Philipp Kappus, Production Manager
Digitalization: the buzzword par excellence – but what does it really mean in the context of operational excellence? We generally understand digitalization to mean the conversion of analogue data into digital formats and systems. In the context of operational excellence, a good data basis is the most important building block. After all, how can you measure key figures and improve them for customer benefit if you don’t have the necessary data?
We speak of a high degree of digitization when a completely paperless operation has been implemented.
Philipp Kappus, Production Manager
For us, digitalization primarily means the introduction of end-to-end information systems, such as ERP, MES and WMS systems. Your ERP system should not only be designed for financial processes, but should also support you in the value-adding processes in your operations. We speak of a high degree of digitalization when completely paperless operations have been implemented – no information should be passed on and documented outside the (integrated) information systems.
In this blog article, my colleague Philipp Carl explains how to select the right ERP system for your company and what you need to look out for. Simply collecting data will not help you achieve operational excellence. You need to use and analyze the data correctly. My colleague Dominik Fackler’s blog article on key figures will help you with this.
Artificial intelligence is omnipresent in the media, at conferences and trade fairs. According to a survey conducted by Bitkom Research in Germany, 66% of respondents believe that artificial intelligence will strengthen the competitiveness of the German economy. As the term AI is defined very broadly, includes a variety of technologies and is sometimes used synonymously with terms such as machine learning, deep learning, supervised learning or neural networks, here is my pragmatic definition:
I understand artificial intelligence as an attempt to replicate certain human decision-making structures. It (currently) always relates precisely to a specific problem and can be used, for example, in automated driving, facial recognition or for weather forecasting. Ultimately, AI supports or relieves the burden on humans.
AI is already commonplace in many areas and will also become increasingly established in operations.
Philipp Kappus, Production Manager
Useful applications of artificial intelligence in operations include the following areas:
Operational excellence requires optimizing the measurement of key performance indicators. These metrics can be captured through algorithms, machine learning or other artificial intelligence applications. Instead of just trying to improve current statistics, operational excellence aims for sustainable optimization.
To illustrate this, here is an example of the use of artificial intelligence in the supply chain: your production planning is too imprecise because your suppliers’ delivery times fluctuate. With the help of AI technology, such as predictive analytics, you can continuously examine and compare your historical data and derive forecasts from it. For example, you can automatically store these in the master data and use them for your planning tools. Your direct benefit is the continuous improvement of the forecast and thus the delivery reliability to your customer.
Most obstacles to the use of AI can be overcome by examining the use of standard software: For example, a suitable choice of standard software can avoid high investment costs, while at the same time guaranteeing the security of your data and therefore data protection requirements.
The benefits of cloud-based working have been clear to see since the coronavirus pandemic at the latest. Let’s take Microsoft Office 365 as an example:
These and many other arguments can also be found for other solutions in your operations. Check the usefulness of each existing and new system and have the options of the software provider or implementation company explained to you.
In many areas, stationary work no longer corresponds to the state of the art.
Philipp Kappus, Production Manager
In contrast to the smart or intelligent factory, the next evolutionary stage – fully autonomous production – does not yet exist. What is the current state of the art in practice?
Until the 1990s, production facilities were only made more flexible through high levels of human resources. Machines carried out individual standardized and predefined work steps. However, the machines worked autonomously and independently. The systems were linked by employees who made the decisions and carried out the work. In a smart factory, all machines and systems are networked with each other via interfaces. This is now standard for new acquisitions, but can also be retrofitted for old machines with a long life cycle.
Before Industry 4.0, machine operators and employees in production sometimes required very good training, as the machines and systems were only designed to be user-friendly to a limited extent. Thanks to new AI methods, such as image recognition and voice dialog systems, machines and processes are adapting more and more to humans. Examples in logistics include systems to support order picking, such as pick-by-light or pick-by-voice. And in production, they can be found in sensors for detecting quality problems, for example. Adapting machines to humans is already cost-effective in many cases today.
These and many other arguments can also be found for other solutions in your operations. Check the usefulness of each existing and new system and have the options of the software provider or implementation company explained to you.
Adapting machines to humans is already economical in many cases today.
Philipp Kappus, Production Manager
In autonomous production, the individual machines and work steps that can produce reliably (by continuously ensuring quality and throughput time) are interconnected in such a way that the products can find their way through production as required. This requires not only providing the information to the machines at the right time, but also continuously simulating production. However, autonomous production does not automatically mean that humans will be replaced. In fact, it is often still more economical to use people for individual work steps. To date, there is no purely autonomous production. However, the introduction of modern MES systems can be the first step in this direction.
Autonomous production currently only exists in theory. However, the introduction of modern MES systems can be the first step towards it.
Philipp Kappus, Production Manager
So-called cyber-physical production systems, which generally have higher cognitive capabilities than purely automated production systems, go one step further. These make it possible to analyze and improve autonomous production planning. At the same time, such systems also generate knowledge. Above all, you can benefit from the independent control of these systems, but also from their high degree of adaptability. The integration of AI also plays a central role in cyber-physical production systems.
Before a specific product is manufactured by a cyber-physical production system, the concept of the digital twin is often used. The system dynamically and independently calculates the parameters required to manufacture the product by comparing them with the digital twin. It also generally checks the feasibility of the product beforehand. Machine learning and the appropriate choice of intelligent sensor technology can also be used here to continuously optimize the production process. Another important feature of such systems is that workpieces or materials are equipped with sensors and actuators and are thus connected to the rest of the system. Connecting all the components of this system via the Internet thus enables decentralized process control – partly by the workpieces themselves.
Before a product is manufactured using a cyber-physical production system, a digital twin is often used.
Philipp Kappus, Production Manager
The use of new technologies is also an important part of operational excellence. A rapid pace of further development and refinement can be observed here. Examples of such technological innovations include the IoT and additive manufacturing processes.
The abbreviation IoT stands for “the Internet of Things”. It is an important component of Industry 4.0 and can help to increase efficiency by automating your entire production process. By networking all your production systems and goods, this enables communication between them and your personnel. In general, the networking of the various integrated production components is based on microprocessors, which provide each of your systems or products with its own address on the Internet. This enables a targeted exchange of data and information between them. The IoT can therefore make a decisive contribution to the automation of your production and processes.
Question your entire production concept and think about disruptive approaches.
Philipp Kappus, Production Manager
By using IoT, sensors and general connectivity in modern production processes, you can gain a large database that enables digital mapping of these processes in real time. This digital image can then be evaluated using cognitive analysis approaches. Decisions in the production process can be made autonomously based on the knowledge gained from this.
The use of digital twins is not limited to certain industries and can be applied throughout the entire supply chain: for example in production, logistics and maintenance. In the area of maintenance in particular, you can use predictive maintenance to determine the condition of your systems more precisely and thus carry out needs-based maintenance. This prevents unexpected breakdowns and thus ensures greater planning accuracy and more reliable production. To further increase efficiency, you can use new LIDAR or FLIR sensors, innovative data standards and suitable IT platforms. A practical tip: talk to the relevant machine suppliers in your industry on an ongoing basis and explicitly visit the stands of innovative start-ups at trade fairs.
You can find more detailed information on the use of digital twins in your supply chain in this article.
Additive manufacturing processes are also being used more and more widely in various areas of industry. Through the targeted use of these manufacturing processes, you can shorten development times and also make the production of complex components more cost-efficient.
Additive manufacturing can minimize the waste generated during the manufacture of products. This often also makes it possible to reduce the amount of energy used. Among other things, it allows you to create significantly more cost-effective prototypes for the development of new products. Additive manufacturing is particularly suitable for small batch sizes, as no special mold is required for production. As a result, you benefit from greater speed and better cost-effectiveness. As additive manufacturing generally requires little or only a few prefabricated parts, this also makes it possible to avoid high stock levels. In addition, you can also use additive manufacturing processes to repair or restore old parts – increasing repeat sales and customer loyalty.
A practical tip: Talk to the relevant machine suppliers in your industry on an ongoing basis and explicitly visit the stands of innovative start-ups at trade fairs.
Philipp Kappus, Production Manager
As digitalization progresses, the requirements for the associated cybersecurity, which is intended to ensure the protection of cyberspace, are also constantly increasing. This includes topics such as cloud computing, big data, IoT and software-based networks.
Nowadays, companies use many different digital applications and programs to optimize processes within the company. However, these are susceptible to being exploited by targeted attacks from third parties. The aim of these attacks is often to access or manipulate data or information. Such attacks can also be aimed purely at disrupting your operations.
Incidents such as the attacks on the EDAG Engineering Group in March 2021 or FAM GmbH in June 2021 show that cyber security should not be underestimated. These events impressively demonstrate the impact that inadequate cyber security can have on you and your company. Just how far-reaching the consequences of such an attack can be is illustrated by the prominent attack on the US IT service provider Kaseya. German companies were also affected. Cyber criminals are also constantly evolving and are now using a wide range of attack methods. These include phishing and malware of all kinds, which you will no doubt have heard of in your private life. The term cybercrime-as-a-service (CaaS) now even refers to the fact that this malware is freely available on the market, almost like normal software.
When it comes to cyber security, your company can also rely on AI and automation for analysis purposes in order to detect and clean up malware at an early stage.
Philipp Kappus, Production Manager
It is therefore important that you strengthen your company’s protection against such attacks in order to prevent data loss or compromise and their often far-reaching consequences. In addition to a heightened awareness of Internet or network security when exchanging data, this also requires you to take direct measures such as involving the entire supply chain and harmonizing standards.
When it comes to cyber security, your company can also rely on AI and automation for analysis purposes in order to detect and clean up malware at an early stage. However, these approaches are also increasingly becoming the target of attacks by cyber criminals and must therefore also be protected. Deep learning algorithms are particularly suitable for this purpose, as they can process large amounts of data efficiently, but are also very robust against attacks themselves.
This article cannot and should not claim to be exhaustive. Nevertheless, I hope to have given you an overview of the current digital trends and buzzwords in the context of OpEx. As the supply chain differs from company to company, I recommend that you examine the use of the various technologies individually and do not rely on generalized assessments.
We constantly monitor the latest trends and technologies and point out potentially useful applications in projects. Depending on the individual use case, we integrate these into our various services in the area of operational excellence.