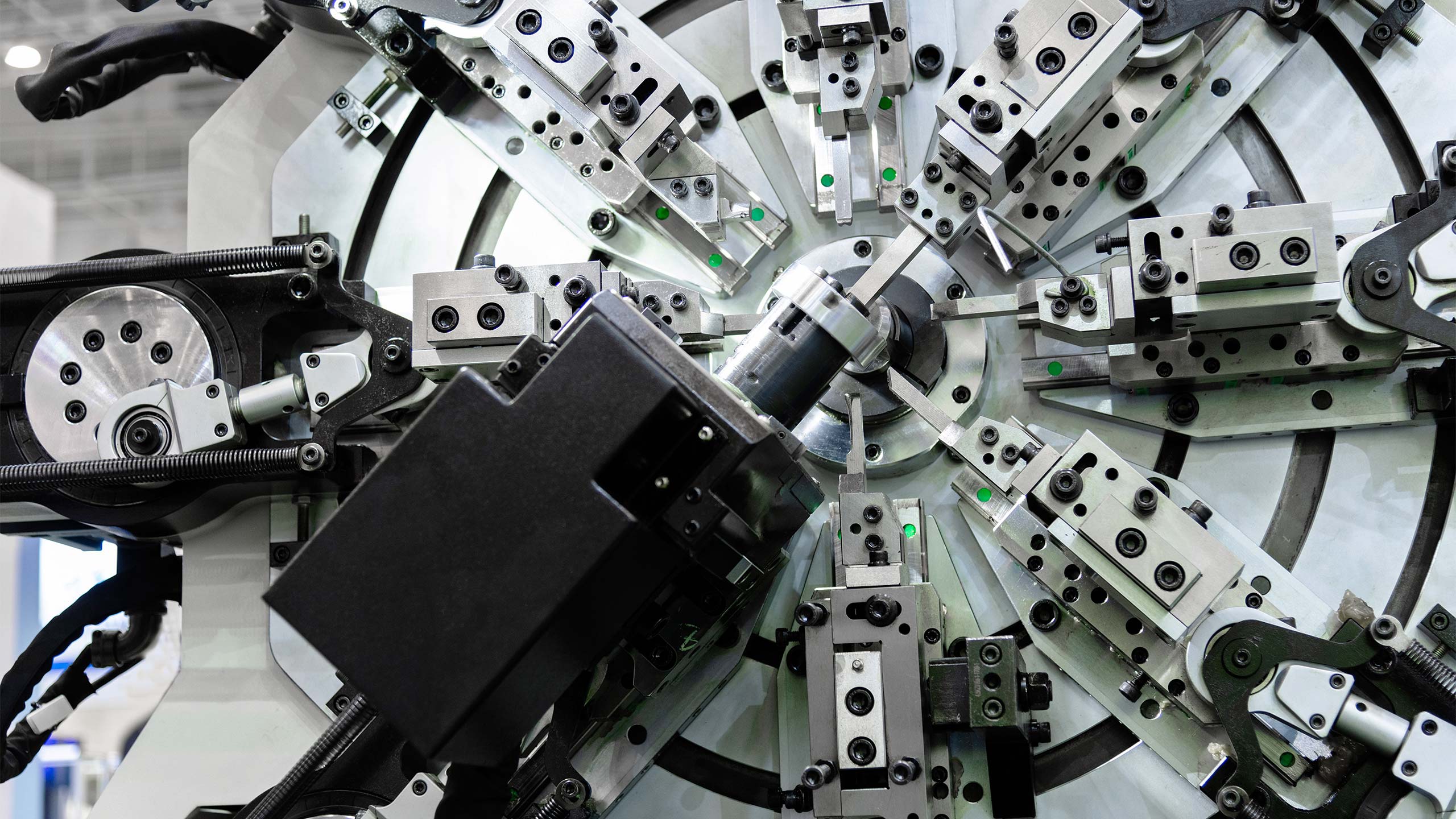
Plant & machinery investment: Replacement investment & expansion investment
The system design phase determines whether a company is also making the best possible economic…
Blog
The digital twin is often used in the context of Industry 4.0 and digitalization. But what exactly is a digital twin? And how can you benefit from it?
Digital twins have been used for some time as images of complex production plants or systems. Recently, digital twins have also been used to optimize the supply chain. We show you the added value of a supply chain digital twin and what you need to bear in mind.
The term digital twin has been around for a few decades. However, it has become particularly popular in recent years, together with the topics of big data and the Internet of Things (IoT). Definitions of the digital twin are as varied as its possible applications. However, all digital twins have some key characteristics in common:
In the following, I will focus on the use of digital twins in the supply chain. In particular, I will show you how a digital twin of the supply chain can support you with numerous problems and issues in supply chain management.
According to the characteristics defined above, a digital twin of the supply chain is a simulation of the company’s own supply chain network. This is supplied with real purchasing, sales and/or shipment data, from which the digital twin generates insights to optimize the network. In principle, this definition applies. However, it is also possible to individually adapt the scope and level of detail of the digital twin to your own requirements.
In its simplest form, for example, the Digital Twin only maps the shipping relations of a regional distribution center to its customers, focusing only on transport costs and transit times. In a complex version, on the other hand, the Digital Twin reflects a 4-stage network, for example: from the supplier, via the production plant, to all distribution locations and from there to all customers via all modes of transport – such as parcel service, general cargo shipping, FTL transport or air freight – including the processes within production and the distribution center.
Accordingly, although the first variant is much easier to create, it has limited informative value. In contrast, the second, complex variant requires a great deal of modeling effort, but offers answers to almost all conceivable questions. Both models are digital twins, provided it is possible to update them with real data in order to gain insights.
The first, simple model could answer the question of how customers can be supplied on the desired date at the best possible cost, while measuring total transportation costs and delivery reliability. The complex model can be used to determine optimal stock levels and required capacities within the distribution locations, define robust replenishment strategies and monitor agreed service levels.
My recommendation for the start: First think about a few specific questions that you want to answer with the Supply Chain Digital Twin so that you can align it with these in the first step. Although it is possible to create a complete picture from the outset, the entry hurdle is significantly higher. With a simple model, you can quickly achieve initial success and convince stakeholders of the benefits of the digital twin. The existing model can then be successively expanded with additional modules.
With a lean model for selected issues, you can quickly achieve initial success and convince your stakeholders of the benefits of the digital twin.
Dr. Clemens Wolf, Manager Digital Operations
Real data is an essential component of a digital twin. Concerns about data quality are unfounded. Most companies with a common ERP system have enough data to create a digital twin in its simplest form: regardless of whether you use SAP, Infor, Microsoft Dynamics, proAlpha or another system.
To model your supply chain, you first need the shipment data with date, receiving address, weight and/or volume and optionally the shipment content. Freight rates and shipping conditions from your transport service provider or the calculation values for your own fleet are also required.
An experienced modeler helps to avoid basic errors and to arrive at an accurate model more quickly.
Dr. Clemens Wolf, Manager Digital Operations
Customer orders, supplier purchases, production orders, stock movements and inventories can be added to enrich the basic model. The more precise your booking points are, the more realistic the model will be. Real-time bookings in the warehouse via handheld terminals and the confirmation of production orders via an MES system offer more detail than retrograde material withdrawal with manual completion booking of the order. But even with the latter, it is possible to record missing times, for example with a value stream analysis or other process recording methods. However, you only need this level of detail if you are interested in the processes within the production and storage facilities of your supply chain.
Once the data basis has been clarified, it is important to select the right modeling tool. At Rothbaum, we currently rely on AnyLogistix software from AnyLogic. Beyond that, however, the market offers plenty of options for small and large, from simple Excel add-ins to complete software suites.
The model forms the core of the Digital Twin and essentially consists of a database with a defined set of rules. The basic data contains information on customers, locations and products. The set of rules defines how the products are procured or produced, which relations are used to transport them to the customers, which order control is used as a basis and which process times and costs are incurred. A large part of the effort is required to create the model. However, an experienced modeler can help to speed up the process.
In order to validate the model created, it is useful to fill it with historical data and simulate the supply chain. The KPIs collected, such as transportation costs and transit times, should correspond as closely as possible to the actual values recorded, apart from minor deviations. Otherwise, the model definition must be readjusted. The data generated by the model is similar in structure to the data generated by the ERP system. You can use solutions that are integrated into the software to analyze the generated data. However, my recommendation is to work with your standard BI tools such as Tableau or PowerBI instead, as these offer a greater variety of options.
The final step is to anchor the created and tested Supply Chain Digital Twin sustainably in the existing IT landscape. Ideally, the model is regularly supplied with new data via an ETL process (Extract, Transform, Load), the model is executed and the results are compiled into ready-made dashboards in a BI tool. The responsible supply chain manager can then use these as a basis for decision-making.
For example, you can align the update frequency with the Sales & Operations Planning process in order to integrate the new sales forecasts into the model on a monthly basis and react to changes in demand. Or you can continuously call up the latest customer orders in order to make short-term operational decisions.
Manager Digital Operations
Would you like to create a Digital Twin or find out more? Send me your message and I will get back to you as soon as possible.
Now that I have given an overview of the function and possible uses of a digital twin, I will summarize the individual components of the digital twin below. I will also discuss the resources required to set up and operate the digital twin.
The model is the brain of the digital twin. This is where the simulation of the supply chain takes place. The model must be created once when you set up the digital twin. To do this, you need modeling software and a modeler that can map the existing supply chain in the software. If changes are made to the supply chain, the model must be adapted accordingly – for example, if new customer markets or locations are opened up, new suppliers are added or new products are launched on the market. As the corresponding changes do not have to be made on a daily basis, you can also rely on external support for this.
The Digital Twin consists of several components that are networked together.
Dr. Clemens Wolf, Manager Digital Operations
The supply chain database merges the model with the real data from your operations. This database is best set up and maintained by your IT or business analytics department. The activities and procedure are comparable to setting up a data warehouse. The requirements, which data is needed and in which form it must be provided, result from the model definition. It is therefore necessary for modelers and database managers to exchange information accordingly.
As soon as the model is supplied with the new data, the supply chain is simulated. In principle, two variants are possible. The model can be executed locally directly in the modeling software. Alternatively, it is possible to export the created model and run it either in the cloud or on a specially hosted server. The cloud or server solution is the better solution for an automated workflow. However, when the first simple models are created, it is also sufficient to run them locally and export the result data manually.
The BI database prepares the results from the supply chain model and combines them with other data sources that are to be used for evaluations. The BI tool of your choice accesses this database in order to visualize the simulated results. The administration of the BI database is also best left to the IT or analytics department.
The final step is the BI dashboard, which visualizes the results from the simulation model, calculates company-relevant KPIs and provides all the information in an understandable way. An experienced analyst with a background in supply chain topics should be responsible for setting up and maintaining the BI dashboard. The individual dashboard elements should be developed in consultation with the supply chain manager. Ideally, all managers who use the results for operational or strategic decisions should be involved.
What previously seemed like a linear process that only worked in one direction is actually a closed loop. The great strength of the Supply Chain Digital Twin compared to pure analysis tools is that the measures or decisions taken can be tested directly and without risk.
Two real examples:
The sales forecast for the next month predicts higher demand than usual. You simulate the model and find out during the evaluation that there is not enough stock to meet demand. You run the risk that your delivery reliability will drop if you do not react in time. Your solution is to increase production for the products in demand.
You consider that you can meet the increased demand with additional shifts. With the adjusted assumptions, you run the model and again realize that the demand cannot be met. You identify a lack of raw materials as the reason for this, as the purchase quantities from the suppliers have not been adjusted. You adjust the model parameters again and simulate the process a third time. Now all KPIs are in the green zone. Your action plan is ready and you forward the necessary tasks to Purchasing and Production.
You are planning to expand in the European market. However, your distribution is bundled at one location. Due to the longer transit times, you are generally unable to offer foreign customers the same level of service as domestic customers. You would therefore like to open a second distribution location abroad and are faced with the question of how best to proceed: Do you rent a warehouse and operate it with your own staff? Do you use a logistics service provider? Or does it make sense to invest in your own building? Where is the best location? What capacities does it need and what additional process steps take place there? What is the best warehousing strategy?
To answer these questions, you can develop various scenarios in your digital twin, determine the performance of each scenario and compare them with each other. This allows you to develop the optimal strategy for you right from the start and avoid costly mistakes during your expansion.
The Digital Twin identifies problems at an early stage and makes it possible to test and compare different solutions without risk.
Dr. Clemens Wolf, Manager Digital Operations
Finally, I would like to present a use case from a past customer project. The task was to design a new distribution center in France. Among other things, the optimal location, the required storage space and employees, the optimal stocks and the processes to be carried out were to be determined. The aim was to improve service levels and save on transportation costs compared to direct delivery from the two existing production sites.
In the first step, we analyzed the required ERP data and recorded the production, shipping and order processing processes on site. The ERP data (delivery bills and customer orders) laid the foundation for the transportation relations. The process recordings were incorporated into the definition of processes and throughput times within the locations. One of the challenges was to merge the ERP data of the two production sites, as two different ERP systems were in use here. We often experience this in comparable projects. However, with the right experience, this challenge can be overcome without any problems.
After creating and validating the baseline model – i.e. the model that depicts the current situation – we worked on the individual issues. With the help of center of gravity models, we determined sensible locations for the new distribution center. We supplemented the results with research into the availability of logistics space and logistics service providers in the identified region.
We initially focused on determining the transportation cost savings and improved transit times resulting from the new location. From numerous projects, we have an extensive database of offers for distribution and logistics services to derive initial assumptions for costs incurred. In the further course of the projects, these are usually validated through a tender.
With the help of Digital Twins, an optimal warehousing strategy was determined.
Dr. Clemens Wolf, Manager Digital Operations
Next, we added the costs for storage and operational activities. We developed one scenario for in-house operation and one for external operation. The solution identified was to use a logistics service provider for the first three years, as this allows more flexibility for short-term adjustments, especially at the beginning of such a project. If the growth forecasts are met from the fourth year onwards, the company should then switch to in-house operation.
It was then necessary to determine the optimum stock levels and the replenishment of these. Particularly in the case of logistics service providers, who charge per used storage space, only as much stock should be stored as is required for optimum operation. Through numerous variation experiments, we have determined the optimum storage strategy. We also examined the extent to which individual customer-specific assembly processes could be carried out at the new location. The aim was to move the creation of variants to the rear and reduce the number of part numbers in the warehouse and thus the storage space required. Min-max stocks were worked out for replenishment in order to enable the best possible utilization of FTL transports from the production sites. We also paid attention to the right balance between transportation costs and warehousing costs.
There are many possible applications for a digital twin. Get in touch with us if you would like to discuss your project.
Dr. Clemens Wolf, Manager Digital Operations
With the help of the Supply Chain Digital Twin, we were able to determine an optimal scenario and demonstrate both cost savings and improvements in delivery times. As the digital twin is permanently linked to the ERP data, it is possible to recalculate the warehousing strategy and adjust stocks accordingly at any time if demand changes.
I hope that I have been able to give you a good overview of the digital twin and its possible applications – and that you now have an idea of the steps you need to take to implement a supply chain digital twin in your company. Of course, there are many more use cases in addition to those described.